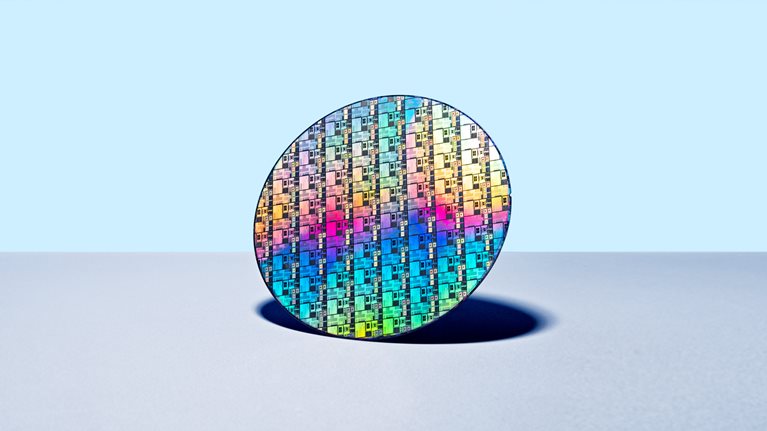
Semiconductors are critical to modern life. According to economic historian Chris Miller, “You can’t understand the modern world without putting semiconductors at the center of the story.” But many people have a murky understanding of what a semiconductor actually is. A first step would be to break down the word. A conductor is something through which electrons freely move from one type of material to another. Have you ever gotten a shock in the winter from touching a doorknob? That’s because metal is a great conductor of electricity. (In fact, so is the human body, which is why you can sometimes pass the shock on to someone else.) The opposite of a conductor is an insulator, which impedes the flow of electrons from one material to another. Rubber is a great insulator, which is why it’s safe to be inside a car (with rubber tires) during a lightning storm.
Get to know and directly engage with senior McKinsey experts on semiconductors
Abhijit Mahindroo is a senior partner in McKinsey’s Southern California office; Bill Wiseman is a senior partner in the Seattle office; Marc de Jong is a senior partner in the Amsterdam office; and Mark Patel is a senior partner in the Bay Area office.
A semiconductor is a class of materials that falls somewhere on the continuum between conductor and insulator. Manufacturers process silicon and other materials into wafers, which are then lithographically printed with various functionalities. The wafer is then cut into the chips that make up semiconductor devices, which enable all kinds of machines to harness electricity for processing power. Semiconductors are in greater demand than ever: The Fourth Industrial Revolution (4IR), which is currently transforming manufacturing, production, and, more generally, global business, is characterized by smart computers and connected devices. Smart means connected, and connected means semiconductors.
While semiconductors can create a wealth of opportunity for industries around the world, reliance on semiconductors could also introduce some vulnerabilities. In this Explainer, we’ll explore the pandemic-era semiconductor shortage, how organizations can mitigate the risks associated with reliance on semiconductors, and why semiconductors stand to dominate the next decade in global business.
Learn more about McKinsey’s Semiconductors Practice.
What’s the potential for the semiconductor industry?
The world of today—and tomorrow—runs on semiconductors. Trends such as remote working, artificial intelligence, and soaring demand for electric vehicles (EVs) are reshaping the world we live in. Accordingly, the global semiconductor industry is poised for a period of growth. McKinsey analysis suggests that industry revenues will climb to $1 trillion by 2030 (exhibit).
About 70 percent of this growth will be driven by just three industries: automotive, wireless, and computation and data storage, with the latter segment as the main source of growth.
What’s the process of manufacturing a semiconductor?
The making, or fabrication, of semiconductors is one of the most complex and sophisticated processes in all of manufacturing. Semiconductor fabrication requires precision down to the nanometer (that’s one-billionth of a meter), atomic ordering, and high chemical purity. And many semiconductor fabrication plants have daily quotas of thousands of wafers and chips.
In the semiconductor industry, the wafer—usually made of silicon—serves as the layer on which materials are processed and formed into chips. Each chip is essentially a highly engineered semiconductor device that is crucial to powering countless electronic devices. As semiconductor technology advances, these chips continue to shrink in size and grow in computing power.
One key process in semiconductor manufacturing is lithography. Lithography involves coating a wafer with a light-sensitive material called photoresist, shining light through a mask (which contains the chip’s pattern) onto the wafer, and chemically developing the exposed areas of the wafer to reveal the pattern. This patterned layer ultimately serves as the guide for building or removing materials in specific regions of the wafer, which determines the final, detailed structure of the chip.
Here are three factors that make semiconductor manufacturing at scale exceptionally challenging:
- Semiconductor manufacturing is iterative. As the wafer moves along each stage of the manufacturing process, it revisits some of the same equipment multiple times. This means that any disruption at any one piece of equipment can create ripple effects at multiple stages of the manufacturing process.
- Semiconductor fabs are large and complex operations. Fabs contain hundreds of linear steps and thousands of iteratively used equipment chambers, each with its own controllers and data streams. Each piece of equipment is managed by efficient and data-driven teams.
- Semiconductor fabs can have a combination of high-volume and high-mix products. As the number of semiconductor-enabled electronic devices increases, fabs are called upon to produce more diverse products at higher volumes. A high mix of different products requires multiple processes to be performed for each product, as well as intricate coordination between planning, engineering, operations, and equipment teams.
Learn more about McKinsey’s Semiconductors Practice.
What are semiconductors made of?
Semiconductors are typically made of silicon, which can become a good conductor of electricity when it’s processed. Silicon is also very stable, which means it can withstand high temperatures. And silicon is abundant: It accounts for about 28 percent of the Earth’s crust.
Over the past few years, semiconductor manufacturers have begun using a wider variety of materials that have particularly advantageous properties for certain applications. These include silicon carbide (SiC) and gallium nitride (GaN) to power electronics in electric cars, indium phosphide (InP) for optical applications, and even diamond as a candidate for applications in space.
SiC and GaN are well-suited to applications that require both high power and frequency because they limit energy loss and allow for the creation of smaller form factors. The push for increased sustainability and electrification is driving the adoption of SiC- and GaN-powered devices, and the annual growth rate for these categories is expected to surpass that of the power semiconductor market as a whole.
How is SiC superior to silicon?
SiC offers improved performance, especially in applications—such as electric vehicles—that require high power. Here are a few ways in which SiC is superior to silicon:
- Higher efficiency. Energy losses are lower with SiC, and thermal management is less expensive.
- Longer lifetime. Better thermal conductivity allows SiC to endure higher stress levels, prolonging the lifetime of the semiconductor device.
- Smaller package. SiC-based devices can deliver similar functionality as silicon-based ones but in a smaller package, which means they can achieve high performance with fewer semiconductors.
- Simpler design. Higher power ranges allow for simpler designs and fewer passive elements.
By 2027, more than 50 percent of battery electric vehicles (BEVs) could rely on SiC powertrains, compared with about 30 percent in 2024. This shift, combined with a growing preference for BEVs among EV buyers, will likely increase demand for SiC.
Which of the world’s regions are specializing in semiconductor manufacturing?
Strong semiconductor ecosystems can be found all over the world. Here are five of the largest:
- At just three square miles in size, Hsinchu Science Park in Taiwan is home to three universities, more than 150 semiconductor companies and suppliers, more than 600 manufacturers, and more than 160,000 highly skilled full-time employees.
- Silicon Saxony, centered in Dresden, Germany, is the largest semiconductor cluster in Europe and contains more than 400 industry actors, universities, and research centers. Over the past 20 years, Saxony has more than doubled the number of employees in the country’s semiconductor industry.
- In South Korea, the cities of Giheung, Suwon, and Icheon are part of the country’s semiconductor mega cluster. The nation plans to invest about $470 billion through 2047 in partnership with major South Korean electronics companies.
- China is also a major producer of semiconductors. Shanghai, Beijing, and the provinces of Jiangsu, Fujian, and Guangdong are all hubs. And China is scaling up fast: Of all the fabrication plants that are currently under construction, about half are in China.
- In the United States, semiconductor companies have announced investments that are estimated to reach $200 billion to $350 billion within the next decade—with the largest investments in Arizona, New York, Ohio, and Texas.
How can semiconductor companies meet soaring demand?
In the semiconductor industry, annual revenues increased 23 percent in 2021—far above the 5 percent increase reported in 2019—and shareholders saw returns that averaged 50 percent as semiconductors helped power the digital revolution.
But looking closer, semiconductor companies are facing significant challenges. Pandemic-era industry shortages (among other reasons) have spurred governments to bring chip manufacturing closer to home. Talent shortages, both in craft labor and engineering-related roles, will need to be addressed. What’s more, chips will likely get more expensive as they are manufactured in less economically advantaged locations. And finding the vast quantities of stable electric power and pure water needed for some semiconductor manufacturing processes isn’t easy.
McKinsey has identified several strategies that may help semiconductor companies improve productivity and understand when they can justify capacity expansion. Here are six critical areas in which semiconductor companies should evaluate their strengths and weaknesses:
- Technology leadership. The companies that can manufacture the smallest, fastest, and most power-efficient devices are likely to come out ahead.
- Long-term R&D. Semiconductor companies have proved that bold, long-term investments can eventually deliver substantial returns that benefit not only shareholders but also society as a whole. For example, creating specialized chips for quantum computing could improve pharmaceutical development and sustainability programs.
- Resilience. The huge disruptions resulting from the COVID-19 pandemic made one thing clear: Resilience is needed in all sectors to weather the uncertainties of the future. Semiconductor companies could work on becoming more agile, which would enable them to respond more quickly to market changes.
- Talent. More semiconductor manufacturing facilities are being developed in new regions, which requires new sources of talent. In addition to increasing their efforts to recruit talent, semiconductor companies should also address the workplace-attractiveness issues that current employees have raised.
- Ecosystem capabilities. Better collaboration with other semiconductor companies could prove useful in addressing challenges related to complex chip design and talent attraction. For example, one company could develop intellectual property and then license it to others.
- Greater capacity. Finally, capacity expansion could benefit some semiconductor companies. But these aren’t easy decisions to make: A new semiconductor fabrication plant takes up to three years to construct and costs about $15 billion. Before proceeding, companies should closely examine the pros and cons of accessing government subsidies, partnering with equipment manufacturers, and other potential cost-saving measures.
If semiconductor companies can focus on these priorities, McKinsey analysis suggests the next ten years could be the “golden semiconductor decade.”
Learn more about McKinsey’s Semiconductors Practice.
How are geopolitics affecting the semiconductor industry?
Given the centrality of semiconductors in modern life, the governments of countries with a semiconductor industry (including China, Japan, South Korea, Taiwan, the United States, and several European countries) are working to ensure against supply chain disruption in an environment of rising competition. Every major country, says economic historian Chris Miller, is investing public money in semiconductors. And companies across the chip supply chain are reckoning with more complex global dynamics than they have in the past, balancing the need for efficient international supply chains with a new trade environment that involves an increasingly complex picture of tariffs and regulations. In the United States alone, public and private investments to expand the semiconductor industry will total more than $250 billion by 2032. Many governments are pursuing a goal of self-sufficiency. But, as Miller says, self-sufficiency is not viable in the semiconductor space, except in some industry niches. That’s because outside of Asia and its strong manufacturing hubs, no single region or country has strong capabilities in any segment of the supply chain.
How can the semiconductor industry manage its emissions as it continues to grow?
Powering the Fourth Industrial Revolution is a critical imperative for the sector, but it’s not the only one. Customers increasingly expect suppliers to reduce their greenhouse gas emissions to achieve a 1.5° carbon pathway. Semiconductor companies have made climate commitments, but at present they’re not enough to limit emissions as required by the 2016 Paris Agreement. Getting the industry to net zero will require more comprehensive, collaborative action.
Here are some steps the industry could take in the short term:
- Gas abatement systems could be installed to transform harmful gases into ones with less global warming potential.
- Heat transfer fluids could be replaced with ones that have less global warming potential.
- Fuel supplies could be substituted with clean options, such as hydrogen or biomass.
In the longer term, semiconductor companies need to shift toward more innovative approaches, making greater investments in decarbonization and showing more willingness to experiment with potential solutions. Collaboration will be helpful here: Companies could develop early-stage decarbonization technologies with start-ups and academic labs, then share them with a consortium of companies.
Learn more about McKinsey’s Semiconductors Practice.
What other challenges are facing semiconductor producers?
In recent years, some segments of the semiconductor industry have grown—such as chips for use in AI and autonomous and electric vehicles—while others have contracted, including chips that are used to power smartphones and computers. Rapidly changing market dynamics can make it difficult for leaders in the industry to set production targets. McKinsey analysis indicates that using analytics to improve existing manufacturing sites can make changes that are often faster, more cost-effective, and more sustainable than expanding manufacturing altogether.
What caused the pandemic-era semiconductor shortage?
About a year into the COVID-19 pandemic, a shortage of tiny silicon chips made big waves in industries throughout the world. In 2021, production assembly lines for everything from smartphones to home appliances to driver-assistance systems ground to a halt. The auto industry was particularly affected: Major carmakers announced significant rollbacks in their production, causing revenue disruptions to the tune of billions of dollars. (This, in turn, triggered an increase in the value of many used cars.)
Here are the factors that contributed to the semiconductor crisis:
- An industry already at full capacity. Known for its cyclicality, semiconductor manufacturing has historically been a boom-and-bust industry. After more than a decade of consolidation, industry conduct became more rational, with capacity additions closely matching growth in demand since about 2016. When the pandemic hit, the industry’s manufacturing assets were operating at close to 95 percent utilization.
- Unexpected changes in demand. The seeds of the auto industry’s semiconductor crisis can be traced to the early days of the pandemic, when auto sales plummeted globally—by as much as 80 percent in Europe. At the same time, demand spiked for personal computers, servers, and equipment for wired communication, which was driven by the shift to remote work. So while automakers’ orders for semiconductors—for use in fuel pressure sensors, digital speedometers, navigation displays, and more—dropped off sharply, personal-electronics manufacturers were ordering more than ever. When the auto sector’s demand recovered in the second half of 2020, the semiconductor industry had already shifted to meet the demand of other types of manufacturers.
- The long road to building new semiconductor manufacturing facilities. Semiconductor fabrication facilities, or “wafer fabs,” take years to build and cost billions of dollars. From the decision to add a new fab, it takes even the most efficient manufacturers more than three years to build the clean room, install equipment, and ramp up production to a high yield.
- Geopolitical tensions. Trade imbalances caused many players to hoard chips, which led to political tensions and increased market pressure.
- Contract terms. Contracts for auto parts generally have shorter delivery times than contracts for parts in other industries. So when the auto industry was ready to place more orders, semiconductor manufacturers were tied up in longer contracts with customers in other industries.
- 5G rollout and overlapping chip demand. 5G technology relies on the same type of semiconductor chips as automobiles. For this reason, automakers may experience continued chip shortages as 5G continues to roll out globally.
Learn more about McKinsey’s Semiconductors Practice—and check out semiconductor-related job opportunities if you’re interested in working at McKinsey.
Articles referenced:
- “Generative AI spurs new demand for enterprise SSDs,” December 3, 2024, Hiroshi Matsubara and Takuya Kudo, with Klaus Pototzky and Mihir Sood
- “Author Chris Miller on the global influence of semiconductors,” October 28, 2024
- “The power of digital: Quantifying semiconductor fab performance,” October 10, 2024, Abhijit Mahindroo, Bill Wiseman, and Ryan Fletcher, with Daniel Mongrain, Mercedes Hill, Shawn Gregory, and Taylor Roundtree
- “Managing uncertainty in the silicon carbide wafer market,” August 6, 2024, Anupama Suryanarayanan, Bharath Aiyer, Bill Wiseman, and Ondrej Burkacky, with Deston Barger, Diana Tang, Julia Dragon, and Wade Toller
- “Reimagining labor to close the expanding US semiconductor talent gap,” August 2, 2024, Bill Wiseman, with Brendan Jay, Nicholas Liao, Taylor Roundtree, and Wade Toller
- “Advanced semiconductors for the era of centralized E/E architectures,” June 19, 2024, Johannes Deichmann, Martin Kellner, and Ondrej Burkacky, with Alina Blos and Fabian Steiner
- “New tactics for new talent: Closing US semiconductor labor gaps,” May 10, 2024, Brendan Jay, Nicholas Liao, Giulietta Poltronieri, Taylor Roundtree, Diana Tang, Wade Toller, and Bill Wiseman
- “Generative AI: The next S-curve for the semiconductor industry?,” March 29, 2024, Ondrej Burkacky, Mark Patel, Klaus Pototzky, Diana Tang, Rutger Vrijen, and Wendy Zhu
- “Exploring new regions: The greenfield opportunity in semiconductors,” January 29, 2024, Ondrej Burkacky, Matteo Mancini, Mark Patel, Giulietta Poltronieri, and Taylor Roundtree
- “Need to boost semiconductor fab efficiency? Look to maintenance,” December 4, 2023, Ryan Fletcher, Yorgos Friligos, Joydeep Guha, and Abhijit Mahindroo
- “Keeping the semiconductor industry on the path to net zero,” November 4, 2022, Sebastian Göke, Mena Issler, Demi Liu, Mark Patel, and Peter Spiller
- “Will the supply–demand mismatch persist for automotive semiconductors?,” October 14, 2022, Ondrej Burkacky, Johannes Deichmann, Michael Guggenheimer, and Philipp Pfingstag
- “How semiconductor makers can turn a talent challenge into a competitive advantage,” September 7, 2022, Ondrej Burkacky, Ulrike Kingsbury, Andrea Pedroni, Giulietta Poltronieri, Matt Schrimper, and Brooke Weddle
- “Semiconductor shortage: How the automotive industry can succeed,” June 10, 2022, Ondrej Burkacky, Johannes Deichmann, Philipp Pfingstag, and Julia Werra
- “Strategies to lead in the semiconductor world,” April 15, 2022, Ondrej Burkacky, Marc de Jong, and Julia Dragon
- “The semiconductor decade: A trillion-dollar industry,” April 1, 2022, Ondrej Burkacky, Julia Dragon, and Nikolaus Lehmann
- “Value creation: How can the semiconductor industry keep outperforming?,” October 15, 2021, Ondrej Burkacky, Marc de Jong, Ankit Mittal, and Nakul Verma
- “Coping with the auto-semiconductor shortage: Strategies for success,” May 27, 2021, Ondrej Burkacky, Stephanie Lingemann, and Klaus Pototzky
This article was updated in April 2025; it was originally published in May 2023.
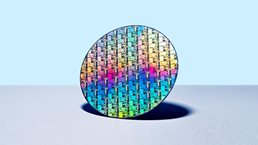